.jpg)
Industrial storage tanks are vital components in various industries, serving as containers for storing liquids, gases, and other substances. Understanding the lifecycle of these tanks, from design to installation, is crucial for ensuring optimal performance, safety, and longevity. In this guide, we'll explore the key stages of the lifecycle of industrial storage tanks and the considerations involved at each step.
Designing Industrial Storage Tanks: Engineering for Efficiency and Safety
The design phase of industrial storage tanks is where functionality, capacity, and safety considerations are meticulously planned. This section delves into the intricate process of designing storage tanks to meet industry standards and regulatory requirements.
Capacity and Dimension: Engineers determine the required capacity and dimensions of the storage tank based on the type of substance to be stored, anticipated usage, and space constraints.
Material Selection: Choosing the appropriate materials is critical for ensuring the durability and compatibility of the storage tank with the stored substance. Factors such as corrosion resistance, structural strength, and temperature tolerance are taken into account during material selection.
Structural Integrity: Design engineers assess structural integrity through rigorous testing and analysis to ensure that the storage tank can withstand internal and external forces, including pressure, seismic activity, and environmental factors.
Safety Features: Incorporating safety features such as venting systems, leak detection mechanisms, and emergency shutdown procedures is essential for preventing accidents and mitigating risks associated with storage tank operations.
Fabricating Industrial Storage Tanks: Precision Manufacturing for Quality Assurance
Once the design is finalized, the fabrication process begins, transforming design blueprints into tangible storage tank structures. This section explores the manufacturing techniques and quality control measures employed during tank fabrication.
Welding and Assembly: Skilled welders meticulously join tank components together using various welding techniques, ensuring structural integrity and leak-free seams.
Quality Assurance: Fabrication facilities adhere to strict quality control protocols to verify the integrity of materials, welds, and components. Non-destructive testing methods such as ultrasonic testing and radiographic inspection are employed to detect defects and ensure compliance with industry standards.
Coating and Finishing: Surface preparation and coating application are critical for protecting the tank against corrosion and extending its lifespan. Specialized coatings are applied to the interior and exterior surfaces of the tank to provide chemical resistance and enhance durability.
Final Inspection: Before leaving the fabrication facility, each storage tank undergoes a comprehensive final inspection to verify dimensional accuracy, structural integrity, and compliance with design specifications.
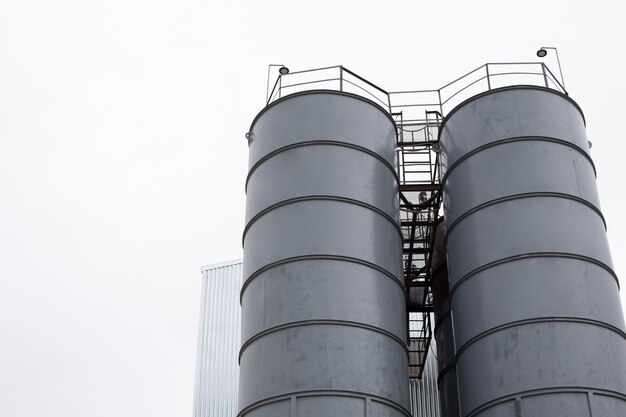
Installing Industrial Storage Tanks: Precision Placement and Integration
Installation marks the final stage of the lifecycle of industrial storage tanks, where careful planning and execution are essential to ensure proper functionality and safety. This section examines the installation process and considerations involved in integrating storage tanks into industrial facilities.
Site Preparation: Site engineers prepare the installation site by leveling the ground, excavating trenches for piping, and ensuring adequate space for crane access and maneuverability.
Transportation and Rigging: Specialized equipment such as cranes and rigging systems are used to transport the storage tank to the installation site and position it securely onto its foundation.
Connection and Integration: Skilled technicians connect the storage tank to piping systems, instrumentation, and control mechanisms, ensuring proper alignment and functionality.
Testing and Commissioning: Comprehensive testing and commissioning procedures are conducted to verify the integrity and performance of the storage tank and associated systems. Functional tests, pressure tests, and leak detection tests are performed to ensure that the tank operates safely and efficiently.
Maintenance and Inspection: Preserving the Integrity of Industrial Storage Tanks
Maintenance and regular inspection are essential to ensure the ongoing integrity and reliability of industrial storage tanks. This section outlines key maintenance practices and inspection procedures to prolong the lifespan of storage tanks and prevent potential issues.
Routine Inspection Schedule: Establishing a routine inspection schedule allows for the timely detection of corrosion, leaks, or structural issues that may compromise the integrity of the tank. Inspections should include visual assessments, non-destructive testing, and evaluation of protective coatings.
Cleaning and Degassing: Regular cleaning and degassing of industrial storage tanks are necessary to remove accumulated sediments, sludges, or hazardous gases that may affect tank performance or pose safety hazards. Cleaning procedures should follow industry best practices and adhere to environmental regulations.
Corrosion Prevention: Implementing corrosion prevention measures such as cathodic protection systems, sacrificial anodes, or protective coatings can help mitigate the effects of corrosion and extend the lifespan of the storage tank. Monitoring corrosion rates and addressing corrosion issues promptly are essential for maintaining tank integrity.
Emergency Response Planning: Developing comprehensive emergency response plans that outline procedures for addressing leaks, spills, or other emergencies involving industrial storage tanks is crucial for mitigating risks and minimizing potential environmental impacts. Training personnel on emergency response protocols and conducting regular drills can enhance preparedness and ensure a swift response to incidents.
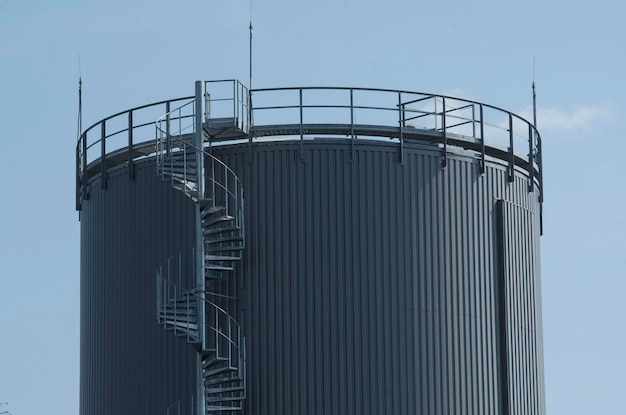
Environmental Considerations: Promoting Sustainability in Industrial Storage Tank Operations
Environmental considerations play a significant role in the design, operation, and maintenance of industrial storage tanks. This section explores strategies for minimizing environmental impact and promoting sustainability in storage tank operations.
Spill Prevention and Containment: Implementing spill prevention measures such as secondary containment systems, leak detection sensors, and spill response kits can help minimize the risk of accidental releases and prevent pollutants from entering the environment.
Waste Management: Proper management of waste streams generated during tank maintenance, cleaning, or decommissioning is essential for preventing contamination of soil, water, and air. Recycling, treatment, or disposal of waste materials should comply with regulatory requirements and environmental best practices.
Resource Conservation: Optimizing water usage, energy consumption, and material inputs in storage tank operations can reduce environmental footprint and conserve natural resources. Implementing water recycling systems, energy-efficient equipment, and sustainable materials can contribute to resource conservation efforts.
Regulatory Compliance: Staying informed about environmental regulations and ensuring compliance with applicable laws and standards is crucial for minimizing environmental liabilities and avoiding penalties. Regular monitoring, reporting, and auditing of storage tank operations are necessary to demonstrate compliance with regulatory requirements.
Upgrades and Retrofitting: Enhancing Performance and Safety of Industrial Storage Tanks
As technology advances and industry standards evolve, upgrading or retrofitting existing storage tanks can enhance their performance, safety, and efficiency. This section discusses common upgrades and retrofitting options for industrial storage tanks.
Leak Detection Systems: Installing advanced leak detection systems such as electronic sensors, acoustic monitoring, or infrared imaging can enhance early detection of leaks and prevent potential environmental contamination or safety hazards.
Remote Monitoring and Control: Implementing remote monitoring and control systems allows operators to monitor tank conditions, control valve operations, and receive real-time alerts remotely, improving operational efficiency and responsiveness.
Safety Improvements: Upgrading safety features such as access ladders, handrails, and fall protection systems can enhance worker safety during tank inspections, maintenance, or emergency response activities.
Environmental Protection Measures: Retrofitting storage tanks with additional environmental protection measures such as secondary containment liners, vapor recovery systems, or stormwater management facilities can mitigate potential environmental risks and ensure regulatory compliance.
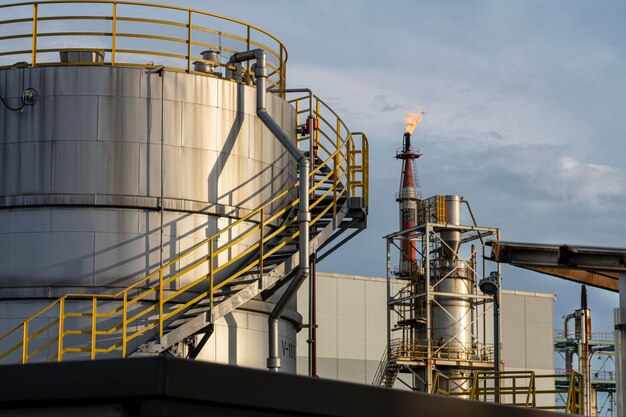
Decommissioning and Disposal: Responsible End-of-Life Management of Industrial Storage Tanks
At the end of their service life, industrial storage tanks must be decommissioned and disposed of properly to minimize environmental impact and ensure safety. This section outlines best practices for decommissioning and disposal of storage tanks.
Tank Cleaning and Decontamination: Before decommissioning, industrial storage tanks must be thoroughly cleaned and decontaminated to remove residual substances and hazardous materials. Proper cleaning procedures should be followed to minimize environmental risks.
Material Recycling and Salvage: Whenever possible, materials from decommissioned storage tanks should be recycled or salvaged for reuse to reduce waste and conserve resources. Metal components can be recycled, while non-metallic materials may be salvaged or repurposed.
Environmental Remediation: In cases where storage tank sites have been contaminated with hazardous substances, environmental remediation measures may be necessary to restore the site to its original condition and mitigate environmental impacts. Remediation activities should be conducted in accordance with regulatory requirements and environmental best practices.
Safe Disposal: Disposal of decommissioned storage tanks should be carried out in compliance with local regulations and environmental guidelines. Proper disposal methods may include dismantling, cutting, or crushing the tank, followed by disposal at authorized waste management facilities. Contaminated materials should be handled and disposed of according to hazardous waste regulations.
Conclusion:
From design to disposal, the lifecycle of industrial storage tanks involves meticulous planning, precision manufacturing, and careful operation to ensure optimal performance, safety, and environmental sustainability. By understanding the complexities involved at each stage of the lifecycle and implementing best practices for design, fabrication, installation, maintenance, and disposal, industry professionals can maximize the lifespan and efficiency of storage tank systems while minimizing environmental impact and ensuring regulatory compliance. Industrial storage tanks play a vital role in supporting various industrial processes and infrastructure, providing essential storage solutions for liquids, gases, and other substances. With proper lifecycle management, these tanks serve as reliable assets that contribute to the efficiency, productivity, and safety of industrial operations.
Write a comment ...